The focus of PERFECT-3D is additive manufacturing to create rapid 3D prints of tooling in support of investment castings. The most common types of 3D printed ceramic parts that we make are ceramic cores, molds, and filters that are often used by foundries that produce investment castings for aerospace and defense applications.
Our Ceramic 3D Printing Services:
Our 3D Print Products
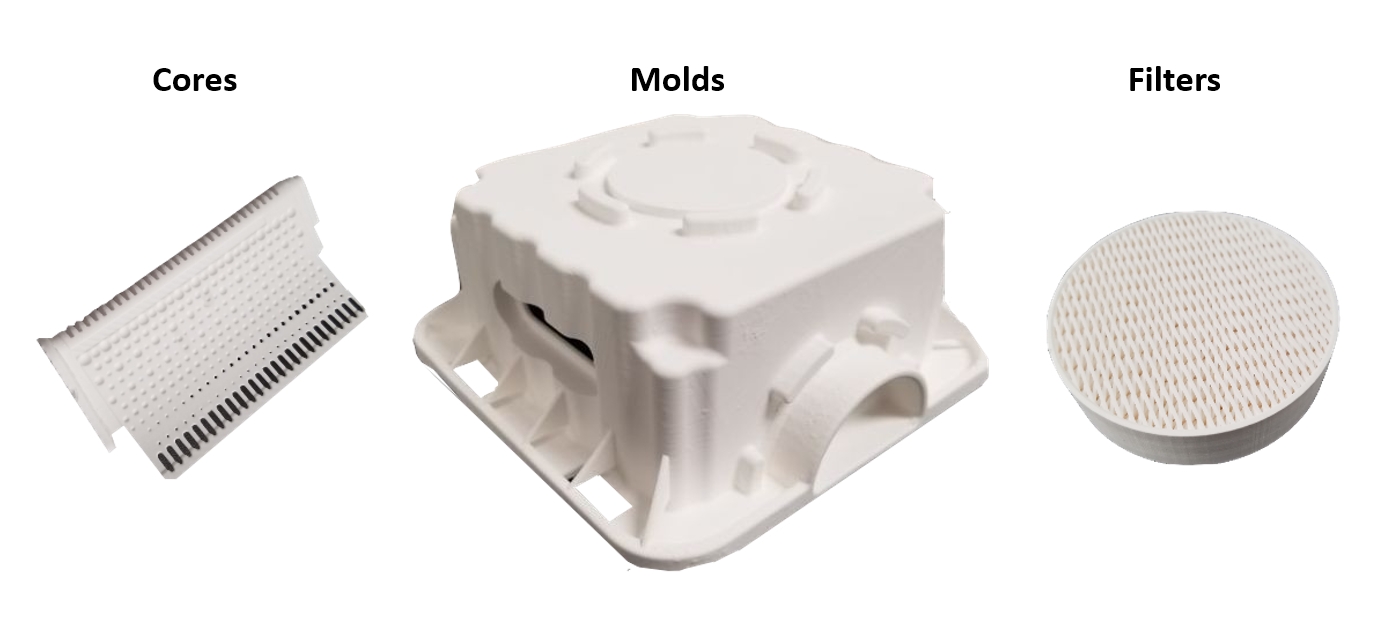
Cores – Ceramic 3D printing can address the complexity of new ceramic core designs that surpass the capability of injection molding. In addition, 3D printing provides a cost-effective and high-performance means to make a small number of cores needed during casting development.
Molds – Ceramic 3D printing can handle the new ceramic casting molds that challenge the traditional ceramic dipping associated with wax patterns. As importantly, the 3D printing of ceramic materials provides ready-to-pour molds that enable “skipping the queue” at the foundry.
Filters – Ceramic 3D printing provides a consistent flow system and material cleanliness that is not achievable with conventional filters. In addition, ceramic filters avoid the introduction of inclusions that are very common with traditional foam filters.
Our Approach on Rapid Prototyping for Production Ceramic Parts
The PERFECT-3D approach is based on leveraging cutting-edge additive manufacturing (AM) to create high-quality tooling for the rapid production of complex parts. Our in-house 3D printing technologies provide other custom industrial 3D printing solutions for customers. More and more industries are realizing the power of the ceramic 3D printer not only for saving time during the prototyping process but also money.
Benefits of the Following 3D Ceramic Parts
3D Printed Ceramic Products
Cost Impact
Cycle Time
Performance
Hard Tooling
Cores
Eliminate expensive non-recurring core die tooling cost
One week from design to first cores compared to multi-month for the conventional approach
Comparable to conventional cores; Our ceramic 3D printers can rapidly iterate designs in days versus months
None required, saving time and money; “CAD as tooling” highly flexible rapid response
Molds
Eliminate expensive wax die tooling cost and eliminate wax patterns
From mold design to casting in 30 days compared to at least 12 months from the conventional cycle
3D printer casting comparable to conventional; no issues with broken wax patterns that cause casting scrap
None required, saving time and money; “CAD as tooling” highly flexible rapid response
Filters
Comparable to current convention filter cost, depending on size and application
Capacity sufficient to meet foundry demands with delivery comparable to convention filters
Tightly controlled flow rates compared to conventional; captures more inclusions than conventional filters
None required; our ceramic 3D printers enable on-demand filters designed to meet high-precision foundry needs
Our 3D Printing Processes Reduce Cost and Lead Time
While ceramic 3D printing is still in its relative infancy, it has the potential to reduce tooling costs for complex precision castings by more than 70%; while also providing an 80% reduction in the lead time for different materials including cores and molds compared to conventional 3D printing processes.
PERFECT-3D’s Manufacturing Process Overview
Click on the image below for a summarized 3-minute video of the PERFECT-3D manufacturing process.
Get Custom Ceramic Components Faster Than Ever Contact Us Today!